铜钼铜材料
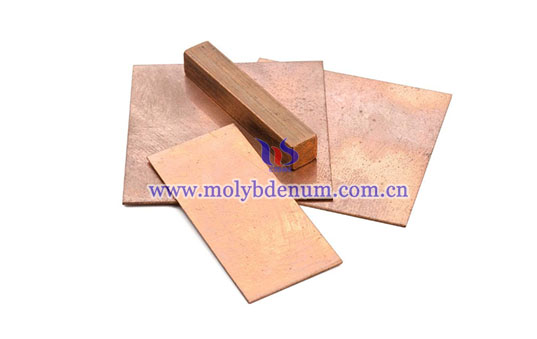
由于铜具有高的导电、导热性能,钼具有低的热膨胀系数、高强度等优点,因此利用两者优异性能组成的复合材料备受电子工程师的青睐,在微电子方面有广泛的应用前景,铜/钼/铜层状材料就是其中的一种]。美国Polymetallurgical,Polese, Elcon等公司采用在线连续轧制复合技术及美国的AMAX公司和Climax specialty metals公司利用热轧复合的方法,生产出了Cu/Mo/Cu(CMC)复合材料,并申请了相关专利,国内也有试验了爆炸复合方法制备CMC电子封装材料的可行性,对爆炸复合CMC封装材料界面的结合机制进行了详细的研究。由于铜和钼的物理性能差异较大,两者互不固溶,因此铜和钼两者界面结合是否牢固是制备铜/钼/铜复合材料的关键,一方面要具有高的界面结合强度,清洁的表面是达到高强度结合界面的一个重要前提。另一方面过于光滑的表面,在大变形量轧制复合时,容易沿着界面滑出,复合强度较低,因此复合前钼板和铜板的表面状态对获得高界面强度的复合材料有着极其重要的影响。
影响Cu/Mo/Cu材料的主要处理方法有:喷砂法、钢刷处理法、化学处理法。
铜/钼/铜的制备采用热轧复合方法,轧制温度为600~1000℃,铜采用高纯1#紫铜板,钼为1#纯钼;其表面处理采用3种不同方法,即喷砂法、钢刷处理法、化学处理法。喷砂法是指钼板先经喷砂后经化学处理去除砂粒、而铜板是用化学处理的表面处理方法;钢刷处理方法是指钼板和铜板都经过钢刷处理;化学处理法是指钼板和铜板表面只经过化学蚀洗。采用SEM,金相组织等方法观察铜/钼界面结合状况。
钼铜合金钼铜合金
化学处理法、钢刷法和喷砂法处理得到的Cu/Mo/Cu复合层板界面平均剪切强度分别为55.9, 66.1和78.9 MPa。显然喷砂法的钼、铜界面间的剪切强度高于化学处理法和钢刷法,而且界面剪切强度的提高对于复合材料防止因热应力循环而导致界面结合失效具有重要意义。从喷砂法处理和化学法处理的退火后金相照片可知,喷砂法的钼/铜界面犬牙交错,表面有起伏;而化学处理方法的铜/钼界面比较平直,因此喷砂法的铜/钼/铜材料的界面结合强度肯定高于用化学处理方法的。另外,由于复合层板退火后退火温度低于钼的再结晶温度,但高于铜的再结晶温度,退火后钼晶粒仍为纤维状组织,而铜则发生了显著的再结晶和长大,与化学法处理的Cu/Mo/Cu复合材料界面附近的铜的金相照片相比,喷砂法处理的复合界面附近铜的等轴晶粒和退火孪晶比较小,铜沿钼、铜界面单位长度上的晶粒比较多,这有利于铜/钼界面剪切强度的提高;而化学处理法的界面附近铜的晶粒比较粗大,退火孪晶多,这对界面剪切强度的提高不利。对于复合材料而言,一般其膨胀系数不同,在受热或降温时,不同热膨胀系数的材料沿复合界面方向伸长或收缩不同,从而产生热应力,两种材料的热膨胀系数相差越大,产生的热应力也就越大,当这种热应力达到一定程度时,就会在结合界面上产生微裂纹,或鼓泡,严重时使得界面大规模分离,导致复合材料失效。实验所研究的Cu/Mo/Cu复合层板主要用于电子封装中的支撑和散热部件,因此要经常承受热应力循环,由于铜的热膨胀系数约为钼的3倍,在受热时,界面上的热应力必然十分显著,钼、铜界面必须具有较高的界面结合强度,才能保证复合层板不致开裂,并稳定可靠的工作。喷砂法处理的Cu/Mo/Cu复合层板在850℃加热并骤冷后并未发现有鼓泡或开裂现象,而化学法和钢刷法处理的材料局部出现鼓泡现象,因此用喷砂法处理的Cu/Mo/Cu复合层板界面结合最牢固,综合性能也更好。